Blog
Insulated Thermal Bottles: A Comprehensive Guide to History, Design, and Sustainability
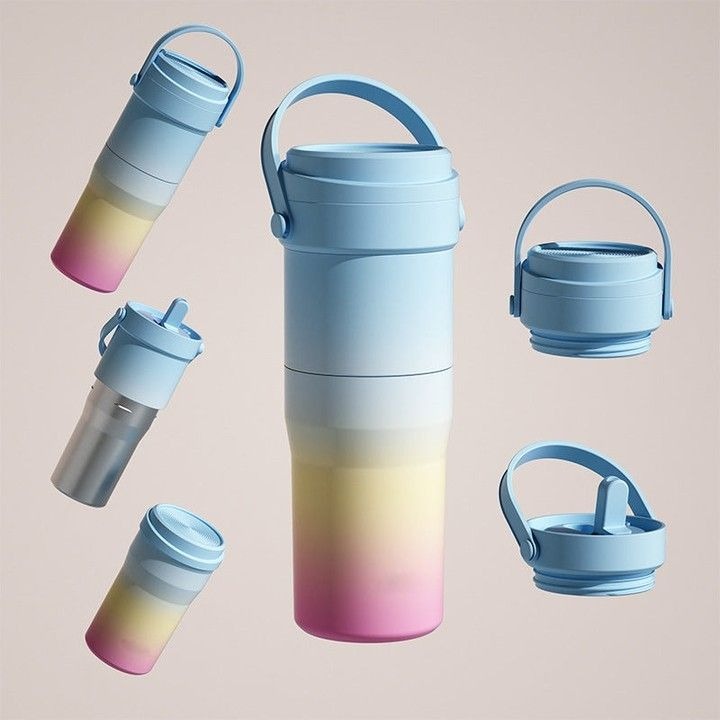
Introduction
In an era defined by mobility, environmental consciousness, and an ever-growing beverage culture, insulated thermal bottles have emerged as indispensable companions for modern consumers. These bottles—featuring vacuum or foam insulation—enable users to enjoy hot coffee, cold water, or even temperature-sensitive meals at optimal warmth or chill far beyond the confines of home or office. This in-depth guide explores the evolution of insulated bottles, examines their engineering principles, highlights cutting-edge materials and designs, addresses health and safety standards, considers environmental and economic impacts, analyzes consumer trends, and offers practical advice for selecting and maintaining the perfect bottle. Through this exploration, we underscore how a seemingly simple container can encapsulate scientific innovation, lifestyle enhancement, and sustainability advocacy.
Origins and Historical Evolution
The story of insulated bottles begins with the vacuum flask invented by Sir James Dewar in 1892. Designed to store liquefied gases at cryogenic temperatures for scientific research, Dewar’s flask consisted of two glass containers nested within each other, with a vacuum between to minimize heat transfer by conduction or convection. Although Dewar did not commercialize his invention, a German company, Thermos GmbH, secured patent rights in 1904 and introduced the first consumer-oriented vacuum flasks under the “Thermos” brand. Early models featured fragile glass interiors encased in metal or woven rattan exteriors to protect against breakage. Throughout the twentieth century, advancements in stainless-steel fabrication and plastic molding gradually replaced glass, making insulated bottles more durable, lightweight, and affordable. By the late 1990s, double-wall stainless-steel bottles with vacuum insulation became widely available, setting the stage for today’s diverse market.
Engineering Fundamentals of Thermal Insulation
At the core of an insulated bottle’s performance lie two key objectives: reducing heat transfer and maintaining temperature stability. Manufacturers employ several strategies:
- Vacuum Insulation: By evacuating the air between the inner and outer walls, producers eliminate most conductive and convective heat transfer. Pressures often fall below 10−3 torr, enabling high-end bottles to retain temperatures for 24 hours or longer.
- Reflective Inner Surfaces: A thin metallic or ceramic coating on the vacuum wall reflects radiant heat, further stabilizing internal temperatures.
- Foam Insulation: Some budget-friendly models use polyurethane or polystyrene foam between walls. Although less effective than a vacuum, foam adds shock absorption and reduces cost.
- Seal Integrity: Precision-molded silicone or elastomer gaskets at the bottle’s mouth prevent air exchange and liquid leakage, preserving vacuum integrity.
- Material Conductivity: Inner chamber materials—typically 304 (18/8) or 316 (18/10) stainless steel—combine low thermal conductivity with corrosion resistance, while the outer shell may use powder-coated steel, BPA-free plastic, or silicone for aesthetics and grip.
Advanced Materials and Design Innovations
Recent years have witnessed remarkable innovation in both materials and form factors:
- Glass-Like Ceramic Liners: Developed to mimic glass’s inert properties without fragility, ceramic coatings provide taste neutrality and resist scratching.
- Aerogel-Enhanced Insulation: Some prototypes integrate silica aerogel—one of the lightest insulating solids—to reduce wall thickness while improving thermal performance.
- Phase-Change Material (PCM) Layers: Encapsulated PCMs absorb or release latent heat at target temperatures, passively stabilizing the contents at specific warmth or coolness.
- Modular Lid Ecosystems: Brands now offer interchangeable lids—ranging from sipper tops and flip-lids to straws and chuggers—allowing users to customize for coffee, tea, smoothies, or water.
- Ergonomic Profiles: Contoured bodies, integrated handles, and collapsible designs (for silicone or polymer models) enhance portability and user comfort.
- Smart Connectivity: Bluetooth-enabled lids track fluid intake, ambient temperature, and remind users to hydrate via smartphone notifications.
Health, Safety, and Regulatory Compliance
Safety is paramount when contacting consumable liquids. Leading manufacturers adhere to stringent standards:
- BPA-Free and Phthalate-Free Certifications: All plastics, coatings, and gaskets meet FDA or EU food-contact regulations, ensuring no hazardous chemicals leach into beverages.
- 304/316 Stainless-Steel Alloys: These alloys are tested for heavy metals (lead, cadmium) and subjected to passivation processes to form inert oxide layers, preventing corrosion and taste alteration.
- Vacuum Durability Testing: Bottles undergo repeated thermal cycling (hot to cold) and pressure testing to confirm vacuum integrity over time.
- Impact and Drop Resistance: Simulated falls from various heights test structural resilience; foam models often outperform vacuum-only designs in shock scenarios.
- Dishwasher and Autoclave Ratings: While many parts are dishwasher-safe, consumers should verify manufacturer recommendations to protect gaskets and exterior finishes.
Environmental and Economic Considerations
In a world grappling with plastic pollution and climate change, insulated bottles contribute to waste reduction and resource conservation:
- Life-Cycle Assessment (LCA): Peer-reviewed studies show that a durable stainless-steel bottle amortizes its production emissions within six to twelve months of daily use, compared to single-use plastic or paper-based containers.
- Recycled and Upcycled Materials: Companies such as Klean Kanteen and Hydro Flask incorporate post-consumer recycled steel, reducing virgin material demand.
- Circular Economy Models: Programs like YETI’s “YETI Rebuild” and S’well’s recycling partnerships refurbish damaged bottles or source end-of-life products for metal recovery.
- Cost-Benefit Analysis: Although initial investment ranges from $20 for basic foam-insulated bottles to over $100 for premium vacuum designs, savings accrue from reduced disposable cup purchases, average café latte costs (around $4–$5), and decreased plastic bottle consumption (approx. $1–$2 per bottle).
Consumer Segmentation and Lifestyle Integration
Insulated bottles now cater to niche markets, reflecting varying priorities:
- Outdoor Enthusiasts: Rugged, oversized bottles (32–64 oz) with metal handles, tether points, and wide mouths for ice and hydration powders.
- Office and Commuter: Slim, cup-holder-friendly designs (12–20 oz), often with integrated tea or coffee infusers and leakproof flip-tops.
- Fitness and Yoga: Lightweight, sweat-proof polymer bottles with straw lids and fruit infuser attachments for flavored water.
- Children and Families: Colorful food jars and toddler sippers with spill-resistant soft spouts and carry loops.
- Tech-Savvy Users: Smart bottles that sync with wellness apps, track hydration goals, and adjust ambient temperature readings.
Selecting the Right Bottle: A Buyer’s Guide
When choosing an insulated bottle, consider the following factors:
- Intended Use: Daily commute, outdoor adventure, or desk use will determine size, mouth width, and lid type.
- Insulation Performance: Check manufacturer’s hot/cold retention claims (e.g., 12 hours hot, 24 hours cold) and verify independent test results if available.
- Material Preferences: Stainless steel vs. ceramic vs. plastic interior; choose based on taste neutrality, weight, and durability.
- Lid Functionality: Screw caps for maximum seal, flip-lids for convenience, straws for easy sipping, or modular lids for versatility.
- Ergonomics and Portability: Handle placement, body contour, and compatibility with bag pockets or bicycle cages.
- Maintenance Requirements: Wide mouth for cleaning ease, dishwasher safety, and availability of replacement gaskets or parts.
- Sustainability Credentials: Look for brands with transparent LCAs, recycled content use, and circular programs.
Maintenance and Best Practices
To extend the life and performance of an insulated bottle:
- Pre-Conditioning: Rinse with hot water for hot beverages or cold water for chilled drinks to stabilize initial temperature.
- Regular Cleaning: Use mild detergent, soft brush, and rinse thoroughly; weekly deep cleans with baking soda or vinegar solution combat odors.
- Component Disassembly: Remove lids, seals, and straws; dry separately to prevent mold growth.
- Avoid Extreme Impacts: Even vacuum bottles can dent or crack under severe drops; consider foam models for rugged use.
- Storage: Keep lids off when not in use to allow ventilation and avoid stale odors.
Future Trends and Technological Frontiers
Looking ahead, innovation will continue to reshape the landscape:
- Nanostructured Coatings: Ultra-thin, durable layers that enhance insulation, scratch resistance, and antibacterial properties.
- Advanced PCM Integration: Tailored phase-change capsules that maintain precise temperatures—ideal for pharmaceuticals, meal prep, or sensitive laboratory transport.
- Renewable Energy Features: Solar-charging surfaces powering low-voltage heating elements or digital displays.
- Smart Materials: Shape-adaptive polymers that adjust vacuum gap under different pressures or temperatures to optimize insulation dynamically.
- Global Regulatory Alignment: Harmonized international standards for safety, materials disclosure, and recycled content verification.
Conclusion
From its humble beginnings in a nineteenth-century laboratory to its present-day role as an emblem of personal style, environmental stewardship, and scientific ingenuity, the insulated thermal bottle stands as a testament to human creativity and conscious living. By understanding the interplay of materials science, design ergonomics, and sustainability principles, consumers can make informed choices that enrich their daily routines, reduce waste, and support responsible manufacturing. As technologies like aerogel insulation, phase‑change materials, and digital connectivity mature, the humble thermal bottle will continue to evolve—offering unparalleled convenience, performance, and ecological value for generations to come.