Blog
The Evolution and Impact of the Insulated Thermal Bottle: An In-Depth Analysis
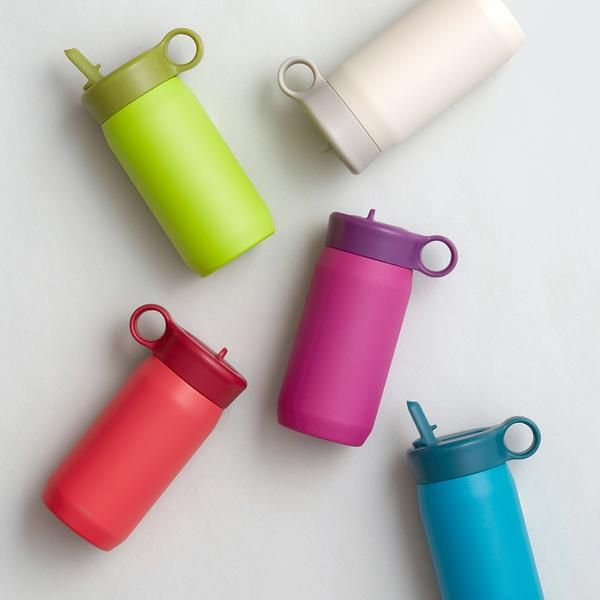
Introduction
The insulated thermal bottle—often referred to as the vacuum flask—has become a ubiquitous tool for modern consumers seeking to maintain beverage temperatures whether at home, in the office, or on the go. What began as a laboratory innovation in the late nineteenth century has evolved into a sophisticated, multi-billion‑dollar industry that intersects design, materials science, environmental sustainability, and lifestyle trends. In this comprehensive essay, we will delve deeply into the historical development, engineering principles, material innovations, health and safety considerations, environmental implications, consumer behaviors, emerging technologies, and future outlook for the insulated thermal bottle. Throughout, we will highlight how incremental improvements and broader cultural shifts have transformed a simple container into an emblem of convenience, sustainability, and personal expression.
Historical Foundations and Early Commercialization
The concept of thermal insulation dates back centuries, but the scientific breakthrough credited with creating the modern vacuum flask emerged in 1892. Sir James Dewar, a Scottish chemist, designed a glass flask within a glass jacket separated by a near-vacuum, drastically reducing heat transfer through conduction or convection. Dewar’s primary aim was to store liquefied gases at cryogenic temperatures for his experiments in physical chemistry. Although Dewar did not patent his invention, the German company Thermos GmbH acquired rights in 1904 and popularized the device under the trademark “Thermos.” Early commercial flasks featured fragile glass interiors encased in protective metal shells or woven rattan covers, making them suitable but delicate for everyday use. Over the next half-century, advances in metallurgy and manufacturing techniques made it possible to replace glass with stainless steel, and fabrics or plastic exteriors replaced rattan, significantly improving durability and affordability.
Core Engineering Principles
To understand an insulated bottle’s performance, one must appreciate its two primary goals: minimizing heat transfer into or out of the container, and preventing radiation effects. Contemporary bottles employ a double-wall construction: an inner chamber and an outer shell, with the interstitial space evacuated or filled with insulating foam. Important mechanisms include:
- Vacuum Insulation: By creating a near-vacuum (pressures as low as 10−6 torr), manufacturers eliminate convective and conductive heat pathways. High-end flasks can maintain temperature differentials for 24 hours or more.
- Reflective Coatings: A thin metallic or ceramic layer on the inner wall reduces radiant heat transfer, reflecting infrared energy back into the contents.
- Seal Technology: Precision-engineered silicone or elastomer gaskets prevent air exchange at the mouth, ensuring the vacuum remains intact.
- Structural Materials: The choice of inner and outer wall materials—typically 18/8 food-grade stainless steel for its corrosion resistance and strength—affects durability, taste neutrality, and weight.
Innovations in Materials and Design
Over the last two decades, manufacturers have introduced a range of novel materials and aesthetic features:
- Glass-Lined Interiors: Some premium bottles use tempered glass linings to eliminate any metallic aftertaste, though these can be prone to breakage under impact.
- Ceramic Coatings: An emerging alternative offering taste neutrality and scratch resistance without the fragility of glass.
- Polymer Overmolds and Silicone Sleeves: For improved grip, impact protection, and tactile variety in color and texture.
- Modular Lid Systems: Interchangeable tops—ranging from leakproof screw-caps to flip lids, straw attachments, and spout-based wide-mouth options—enhance versatility for different beverages and activities.
- Ergonomic Shapes: Contoured profiles, integrated handles, and expanded base diameters improve stability and user comfort.
Health, Safety, and Regulatory Standards
Consumers demand assurance that their thermal bottles are free from harmful chemicals and microbiological risks. Standards and practices include:
- BPA-Free Certification: Ensures plastic or polymer components do not leach bisphenol A or related compounds.
- Food-Safe Alloys: Stainless steels such as 304 (18/8) or 316 (18/10) grades are tested for heavy metal content and passivated to resist corrosion.
- Pressure and Drop Testing: Bottles undergo simulated real‑world stresses to verify vacuum integrity and structural resilience under falls or impacts.
- Microbial Control: Wide-mouth openings, detachable components, and dishwasher-safe ratings facilitate thorough cleaning and sanitization, reducing mold or bacteria buildup.
Environmental and Economic Impact
Single-use plastic waste has emerged as a global crisis: more than 8 million metric tons of plastic enter the world’s oceans annually. Reusable thermal bottles offer a tangible method for individuals to reduce their plastic footprint:
- Life‑Cycle Assessment (LCA): Research indicates that a single high-quality stainless‑steel bottle can offset the carbon emissions of its production after approximately six months of daily use compared to typical plastic bottles or paper cups with plastic liners.
- Recycled Content Programs: Leading brands such as Hydro Flask and Klean Kanteen incorporate post‑consumer recycled steel or plastic in their products.
- Circular Economy Initiatives: Some companies provide trade‑in or refurbishment services, ensuring end-of-life bottles are recycled rather than landfilled.
- Cost Savings: Although initial purchase prices range from $20 to $50, routine use can save hundreds of dollars annually by eliminating disposable containers and expensive café purchases.
Consumer Behavior and Market Segmentation
The insulated bottle market has diversified to address various demographics and use‑cases:
- Outdoor and Adventure: Rugged bottles targeting hikers, campers, and athletes often feature enhanced shock resistance, carabiner-compatible handles, and hydration‑oriented lids.
- Professional and Commuter: Sleek, low-profile designs sized to fit car cup holders and office desks, often with integrated tea or coffee infusers.
- Family and Pediatric: Brightly colored, lightweight food jars and bottles with spill‑proof sippers designed for children.
- Health and Wellness: Smart bottles with embedded temperature sensors, hydration‑reminder timers, and even Bluetooth connectivity to sync water intake data with mobile apps.
- Lifestyle and Fashion: Collaborations with artists, limited‑edition colorways, and personalized engraving options cater to style-conscious consumers.
Case Studies: Brand Strategies
- YETI: Launched in 2010 with heavy-duty coolers, YETI disrupted the insulated bottle segment through aggressive branding and price premiums exceeding $100. Their success rests on the perception of professional-grade durability and aspirational outdoor lifestyle marketing.
- Hydro Flask: Emphasizes community engagement and environmental stewardship through partnerships with non‑profits, coupled with a broad color palette and accessories ecosystem.
- Stojo: Introduced collapsible, silicone‑based drinking containers for urban commuters, focusing on packability and convenience in small bags and purses.
Emerging Technologies and Future Directions
Material science and digital integration are set to further transform thermal bottles:
- Aerogel Insulation: Ultra-light, highly porous materials that could outperform vacuum technology at lower production costs.
- Phase‑Change Materials (PCM): Embedded layers that store and release thermal energy at specific temperatures, offering passive temperature regulation without external power.
- Solar‑Powered Self‑Heating: Early prototypes integrate thin-film solar cells and resistive heating elements, enabling beverages to be reheated outdoors without external power sources.
- Biodegradable Polymers: Next-generation bioplastics derived from algae or agricultural waste may replace conventional plastics in caps and seals.
- IoT and Data Analytics: Connected bottles capable of tracking fluid intake patterns, ambient temperature, and nutritional content, feeding personalized recommendations into wellness ecosystems.
Practical Implications and Best Practices
To maximize performance and longevity, users should adopt best practices:
- Pre‑Heating and Pre‑Cooling: Rinse the bottle with hot water or ice water before filling to reduce initial temperature losses.
- Moderate Fill Levels: Avoid overfilling to prevent pressure buildup and maintain optimal vacuum space performance.
- Routine Cleaning: Disassemble all parts weekly; sanitize with baking soda or a mild bleach solution as needed.
- Avoid Abrasives: Use non‑abrasive brushes and cloths to preserve interior coatings and external finishes.
Conclusion
From its laboratory origins in the work of Sir James Dewar to the dynamic global market of today, the insulated thermal bottle symbolizes how a straightforward scientific principle—thermal insulation—can drive technological innovations, sustainable practices, and cultural trends. With ongoing research into advanced materials, digital integrations, and circular‑economy models, the next decade promises to further elevate the performance, ecological credentials, and personal utility of these versatile vessels. As consumers become more conscious of environmental impact and lifestyle optimization, the insulated bottle will continue to adapt, offering a blend of functionality, sustainability, and individualized expression that enriches everyday routines around the world.